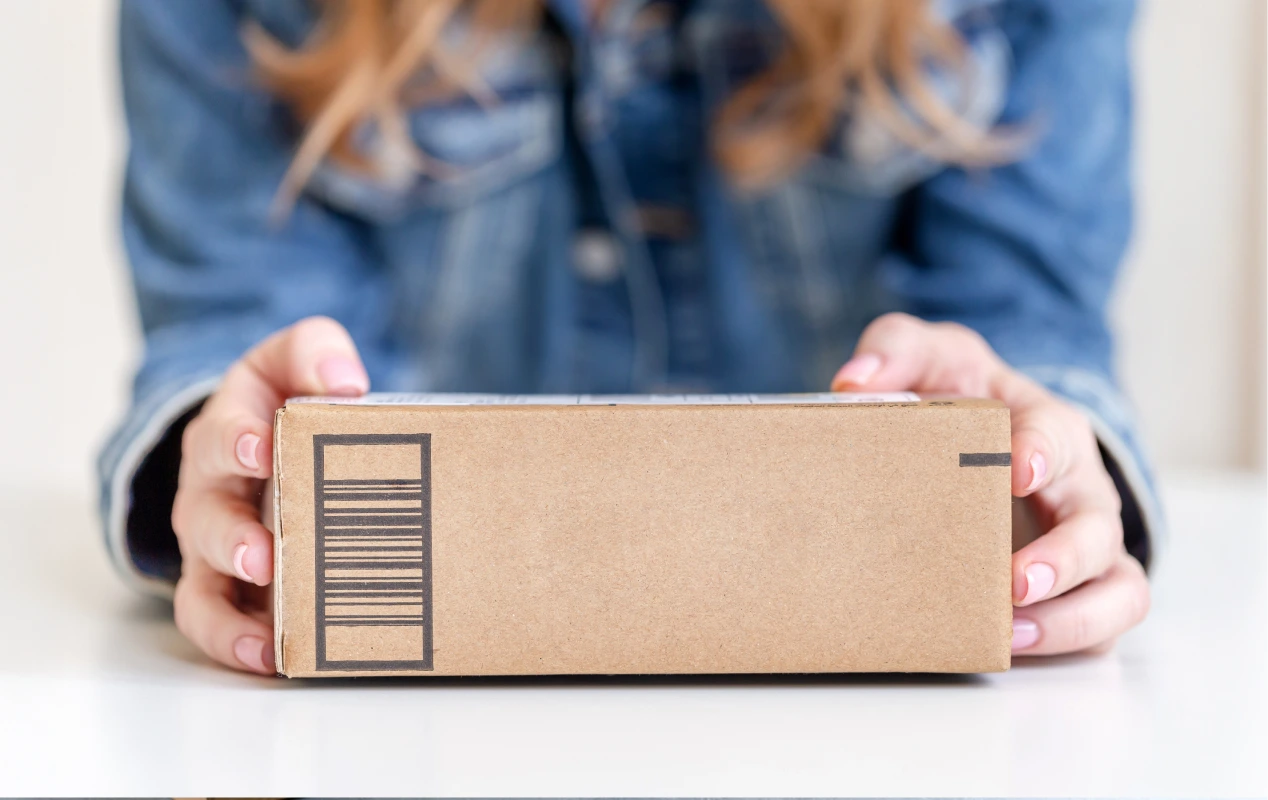
8 mins read
3 mins read
Imran Kermalli
January 15, 2016When operating a small business, you're always looking for different angles to decrease spending and increase your bottom line and it's not always easy, or obvious for that matter. Whether you're trying to cut back in one area, or increase sales or margins in another, every piece adds up at the end of the year so you want to try your best to stay ahead of it all.
Shipping and logistics is a one of those less-obvious departments that you can easily improve by a tenfold to increase your bottom line. Check out these 10 shipping and logistics best practices that you should be utilizing today to start increasing your profitability.
It may be wise to start a compliance program and even hire a full time compliance" manager to ensure that your vendors are meeting requirements for your business to succeed in its supply chain.
A well run facility will scan and record it as a transaction whenever a product moves. Be sure to do this so you can keep accurate inventory data.
You should consider using automated systems for printing, labeling and sealing or taping. The idea is to eliminate steps or touches in your various fulfillment processes.
Utilize bar code and radio frequency identification (RFID) systems to reduce errors in picking and lower labor costs while increasing efficiency.
Maintain a dedicated space for returns so that a return manager can determine what can be returned to stock, what can be repaired, and what needs to be sent to the trash.
Use a continuous cycle counting program (perpetual inventory system) to eliminate having to do actual physical inventory checks.
Look to use hands free picking technology like voice picking devices that save your employees massive amounts of time.
Be careful on how you select and determine metrics.
Take an order picking accuracy example: Your selectors pick 1,000 units, and in one order, pick two of Item A instead of two of Item B. Some customers may identify that as two errors, and say you've shipped two of the wrong item, achieving 99.98-percent accuracy.
However, it could also be four errors, or 99.96-percent accuracy, as you've overshipped two of Item A, and undershipped two of Item B. This, in effect, creates four errors for the customer.
Look at your customers needs every few months and adjust the design of your shipping and logistics system to work best based on that alignment.
Continue to adjust your slotting positions based on demand and seasonality. That way your fast sellers are in positions where they can be picked quickly.
By using these best practices, you can optimize your shipping and logistics processes to become more efficient in your business.
Please contact us for more business tips to improve your shipping and supply chain management. We'll come up with the perfect shipping & logistics solution for your business.